Understanding Tube Fitting Dimensions: A Comprehensive Guide
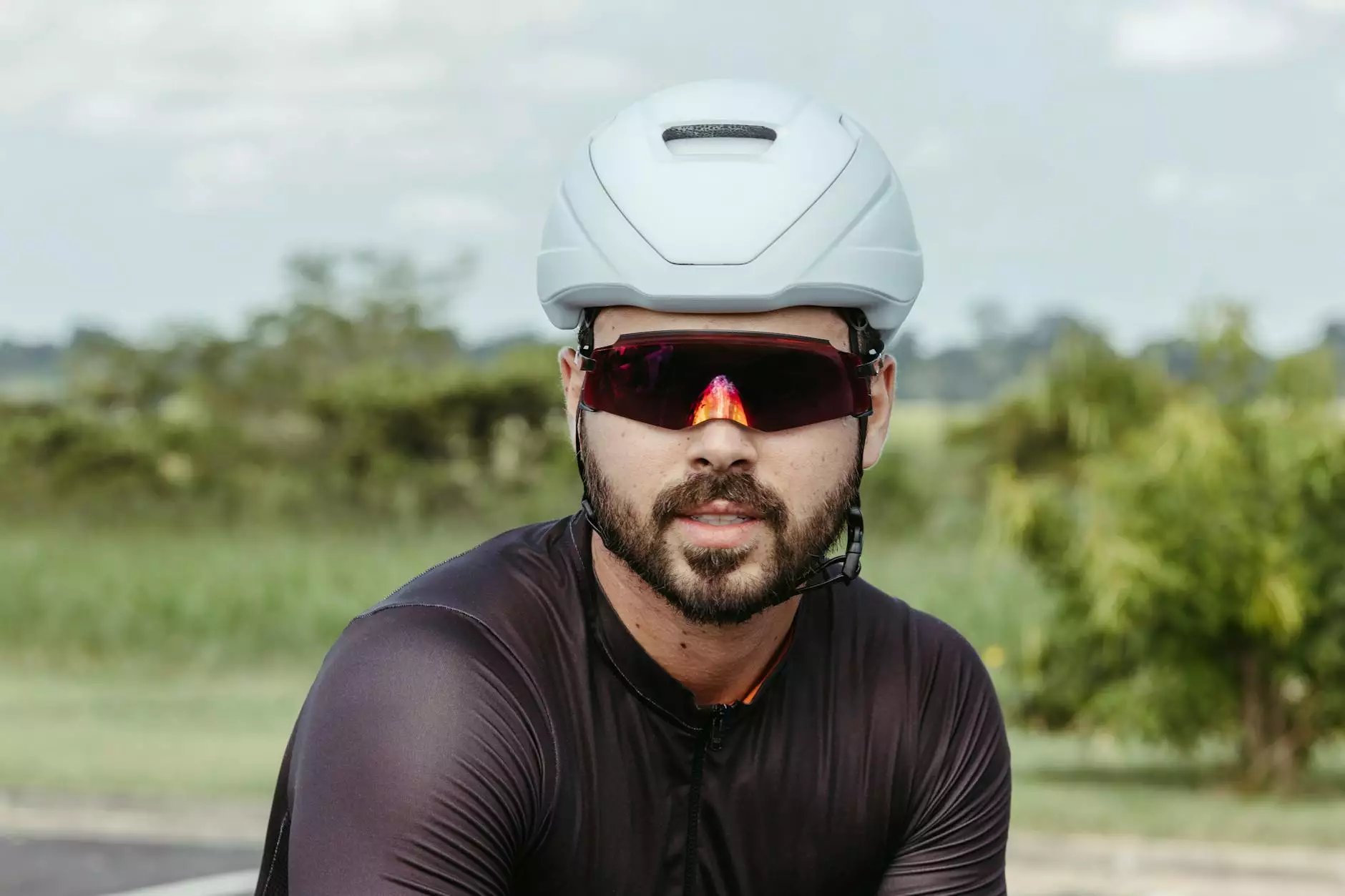
The importance of accurate tube fitting dimensions cannot be overstated in today's industrial and manufacturing environments. Properly sized and designed tube fittings ensure optimal performance, safety, and efficiency in numerous applications. In this detailed guide, we will explore the various aspects of tube fittings, including their dimensions, types, and applications across different sectors. Our goal is to provide you with comprehensive insights that can aid in making informed decisions for your projects.
What Are Tube Fittings?
Tube fittings are essential components in fluid transfer systems. They connect sections of tubing, assist in regulating fluid flow, and help manage pressure within systems. Tube fittings are widely used across various industries, including:
- Oil and Gas
- Aerospace
- Automotive
- Pharmaceutical
- Food and Beverage
These fittings come in various designs, each tailored to specific functionalities and environments. Understanding the dimensions of tube fittings is crucial for achieving seamless connections and optimal system performance.
Types of Tube Fittings
Tube fittings are categorized based on their construction and connection methods. Here are some common types:
- Ferrule Fittings: Utilizing a ferrule, these fittings create a strong cylindrical seal when pressure is applied. They are favored for their reliability and ease of use.
- Forged Pipe Fittings: These fittings are made by forging metal and are known for their strength and durability, making them suitable for high-pressure applications.
- Threaded Pipe Fittings: These fittings use threads for connection and are commonly used in home plumbing as well as industrial applications.
- Flanges: Used to connect pipes, flanges provide a robust seal and are easily maintained, allowing for quick disassembly.
- Check Valves: These valves prevent backflow in systems, allowing fluid to flow in one direction only.
- Ball Valves: Ideal for quick isolation, ball valves provide full flow and excellent sealing.
The Importance of Accurate Tube Fitting Dimensions
When implementing tube fittings in any system, precision in dimensions is vital. Here are some reasons why:
- Safety: Incorrect dimensions can lead to leaks or catastrophic failures, posing risks to personnel and property.
- Performance: Properly sized fittings contribute to the efficiency of a system, reducing energy loss and enhancing throughput.
- Compatibility: Understanding the dimensions ensures compatibility with existing systems and components.
Key Tube Fitting Dimensions to Consider
The following dimensions are critical when selecting tube fittings:
- Outer Diameter (OD): This is the measurement of the outermost part of the tube. It’s essential for ensuring a proper fit with the fitting.
- Inner Diameter (ID): The inner diameter impacts flow rates and pressure within the tube. Correct ID is essential for maintaining system efficiency.
- Wall Thickness: This dimension affects the strength and durability of the tube. Thicker walls generally provide better resistance to pressure.
- Length: The length of the fitting, especially for adapters and connectors, impacts installation and overall system design.
Measuring Tube Fitting Dimensions
Accurate measurement of tube fittings involves several techniques:
- Calipers: Precision calipers are commonly used to measure both OD and ID accurately. Adjusting the calipers correctly is critical to achieving precise measurements.
- Micrometers: For precise wall thickness measurements, a micrometer is ideal as it offers a high degree of accuracy.
- Measuring Tape: For longer fittings, a flexible measuring tape can provide an adequate way to gauge length without causing damage.
Common Applications of Tube Fittings
Tube fittings find applications in various fields, each necessitating specific dimensional requirements:
- Hydraulic Systems: High-pressure environments require precise dimensions for safe and efficient operation.
- Medical Equipment: In pharmaceutical applications, hygienic fit and integrity are paramount.
- Manufacturing: Streamlined production processes rely on accurate dimensions to ensure smooth operations.
Choosing the Right Tube Fitting Dimensions
When selecting the appropriate tube fitting dimensions, consider the following tips:
- Understand System Requirements: Analyze the specific requirements of the system, including pressure, flow rates, and environmental conditions.
- Consult Manufacturer Specifications: Always refer to the specifications provided by the manufacturer to avoid errors in size selection.
- Test Components: If possible, cross-verify the dimensions with existing components to ensure compatibility.
Conclusion
In conclusion, understanding tube fitting dimensions is crucial for successful implementation in any fluid transfer system. With numerous types available, each serving specific industries and applications, the need for precise measurements cannot be overlooked. Investing time in learning about and measuring the appropriate dimensions can lead to improved safety, efficiency, and performance in your systems.
For more information or to explore a wide range of high-quality tube fittings, visit us at techtubes.in.